Kühlhaus Neuhof AG, CH-Gossau
Erweiterung automatisches TiefkühllagerDie Kühlhaus Neuhof AG in Gossau wurde 1977 gegründet und ist als Lagerhaus im Tiefkühlbereich tätig. Sie ist spezialisiert für die Einlagerung von Fleisch, verarbeiteten Kartoffeln, Gemüsehalbfabrikaten und Lebensmitteln aller Art. 2010 ist ein Neubau mit rund 5'780 Palettenplätzen erbaut und 2012 in Betrieb genommen worden. Die Gilgen Logistics lieferte damals die Palettenfördertechnik, sowie die LKW-Andockstationen.
Im TK-Lager werden vor allem Dienstleistungen im Bereich Lebensmittellagerung und –umschlag angeboten. Verschiedene Kunden (Teilhaber und Dritte) nutzen die Logistik-Dienstleistung zur Auslagerung ihrer Produktionsmengen oder als Zwischenlagerung für Rohstoffe.
Die mit dem damaligen Neubau realisierte Verdoppelung der Kapazität wurde entgegen den Erwartungen bereits gegen Ende des zweiten Betriebsjahres erreicht. So konnte den Einlagerungswünschen der Geschäftspartner nur noch beschränkt nachgekommen werden. Nur 5 Jahre später werden die Räumlichkeiten rund eineinhalb Mal so gross wie der bisherige Bau sein.
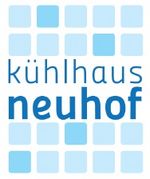
Erweiterung des Tiefkühllagers
Die Gilgen Logistics AG wurde für diese Erweiterung des Tiefkühllagers beauftragt. Die Kapazität des bestehenden Hochregallagers wird von 5'780 auf über 13'100 Palettenplätze mit zwei weiteren Lagergassen (1 Regalbediengerät doppeltief / 1 Regalbediengerät mehrfachtief mit Kanalfahrzeug) erhöht.
Die Produktlagerung erfolgt im vollautomatischen Hochregallager bei einer Temperatur von ca. -28° C. Die Palettenfördertechnik mit 2 Aufzügen wird im -28°C Temperaturbereich und teilweise im Schockfrostbereich -38°C installiert. Des Weiteren liefert Gilgen die Steuerung, das Lagerverwaltungssystem, sowie der Materialflussrechner für die neue Logistikanlage. In einem Teil des Lagers werden in zwei Stockwerken manuelle Kommissionierbereiche eingebaut. Weiter installiert Gilgen ein Vorbau mit zwei Andockrampen und einer Aussenrampe.
Nebst der Erweiterung des Hochregallagers werden auch Optimierungen an der Logistiktechnik im heutigen Lager vorgenommen. So wird es in Zukunft auch möglich sein, Paletten zwischen dem bestehenden und dem neuen Hochregallager zu verschieben. In Zukunft wird ein grosser Teil des Energieverbrauches vom Tiefkühllager mit Elektrizität aus der neuen Photovoltaikanlage gedeckt.
Die Kühlhaus Neuhof AG in Gossau hat mit einem rund 17 Millionen teuren Erweiterungsbau die Kapazitäten für die Lagermenge weit mehr als verdoppelt. Ausserdem werden neue Dienstleistungen wie das Schockgefrieren, das Antauen oder das Kommissionieren angeboten. Am 21.02.2019 lud das Kühlhaus zur Eröffnung des Erweiterungsbaus ein.
Weitere Referenzen
Lebensmittel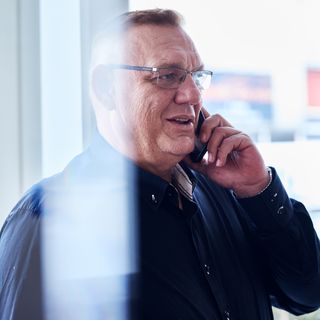